Imagine having a virtual replica of your entire manufacturing process, where you can monitor and optimize operations in real-time. Digital twins are doing just that, transforming how you approach efficiency, maintenance, and decision-making. By harnessing data analytics and advanced technologies, you can greatly reduce downtime and innovate like never before. But what does it take to implement a digital twin effectively? And how can future trends like AI and blockchain further revolutionize this concept? Let’s explore these questions and uncover the potential of digital twins in manufacturing.
Key Takeaways
- Digital twins enable predictive maintenance, significantly reducing downtime and maintenance costs.
- They optimize manufacturing processes, enhancing efficiency and resolving bottlenecks.
- Digital twins facilitate resource optimization, minimizing waste and improving material utilization.
- They drive innovation by allowing new ideas to be tested virtually without disrupting production.
- Digital twins provide real-time insights into supply chains, improving decision-making and reducing risks.
Types of Digital Twins
What’re the different types of digital twins that can revolutionize manufacturing processes? You’ll find that digital twins span various aspects of manufacturing, from design simulation to supply chain monitoring.
First, Product Twins are virtual replicas of individual products or components used for design simulation and testing. They allow you to predict and optimize performance before actual production begins, minimizing costly errors.
Next, Asset Twins are digital representations of physical assets like machinery and equipment. They integrate real-time sensor data and historical performance data to enable asset optimization, ensuring you extract maximum value from your equipment and reduce downtime through predictive maintenance.
Then we’ve Process Twins, which are digital models of manufacturing processes and workflows. These twins drive process efficiency by allowing you to simulate, analyze, and optimize production lines. With process twins, bottlenecks can be identified and resolved swiftly, ensuring a smoother production flow.
Factory/Plant Twins offer a holistic digital replica of an entire manufacturing facility. They integrate various data sources across the plant, giving you a complete view of operations. This 360-degree perspective helps in optimizing overall factory performance and energy utilization.
Lastly, Supply Chain Twins and Inventory Twins revolutionize supply chain monitoring and inventory management. Supply Chain Twins provide real-time visibility into the entire supply chain network, from suppliers to distribution. They help in risk mitigation and improved decision-making through data-driven insights.
Inventory Twins, on the other hand, simulate and optimize inventory levels across warehouses and distribution centers, ensuring you meet demand while minimizing excess stock.
Benefits for Manufacturing
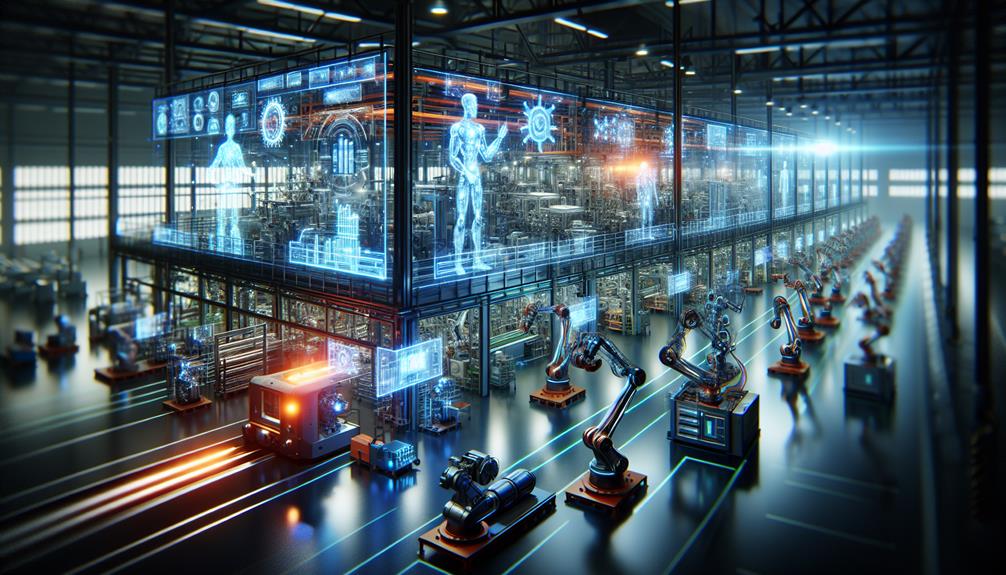
Harnessing digital twins in manufacturing yields significant benefits, including enhanced efficiency, reduced downtime, and optimized resource utilization. When you implement digital twins, you’re not just creating a virtual replica; you’re tapping into a powerful tool for improved efficiency and substantial cost savings.
Digital twins enable predictive maintenance by continuously monitoring your machinery and equipment. By utilizing real-time data analytics, you can anticipate potential failures before they occur, reducing downtime and maintenance costs. You’ll be able to schedule repairs at ideal times, guaranteeing that your production lines remain operational and efficient.
Data analytics play a pivotal role in process optimization. Digital twins collect and analyze vast amounts of data from various sensors and systems within your manufacturing setup. This data provides actionable insights, allowing you to pinpoint inefficiencies and optimize processes. Whether it’s adjusting production schedules or fine-tuning equipment settings, the data-driven approach ensures you’re operating at peak efficiency.
Furthermore, digital twins support resource optimization by providing an in-depth view of your manufacturing operations. You’ll be able to simulate different scenarios and their potential impacts, helping you make informed decisions about resource allocation. This leads to reduced waste and better utilization of materials, ultimately contributing to cost savings.
Incorporating digital twins into your manufacturing processes also enhances your ability to innovate. With virtual replicas of your products and processes, you can test new ideas and designs without disrupting your actual production. This accelerates the development cycle and brings innovative products to market faster.
Digital Twin Case Studies and Examples
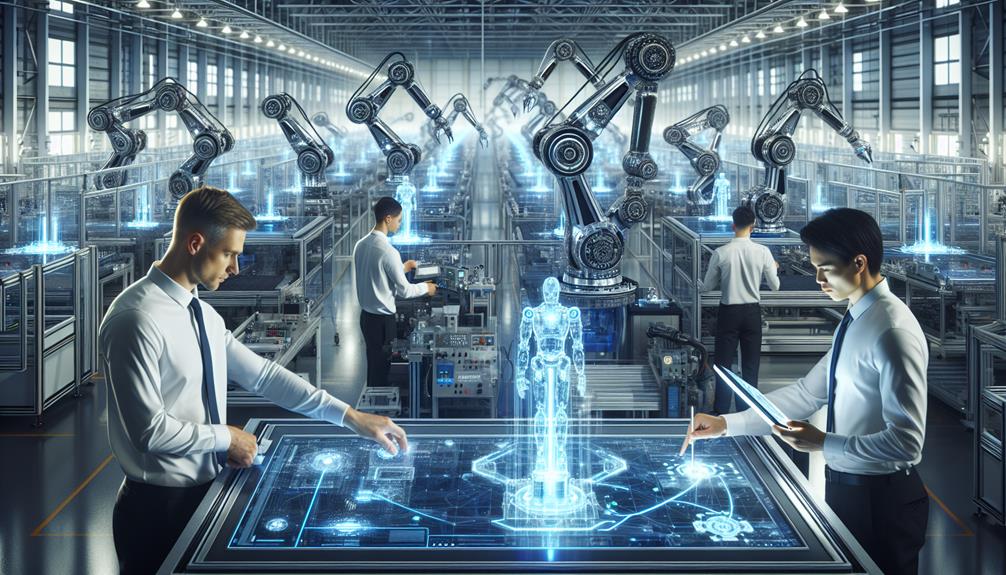
Building on the significant benefits digital twins bring to manufacturing, let’s explore real-world case studies and examples that demonstrate their transformative impact. These examples illustrate how digital twins are implemented and the impressive performance results they yield.
Consider the case of Siemens. They utilized Product Twins to simulate and optimize the design of their gas turbines. This implementation strategy enabled them to predict and mitigate potential issues, enhancing product quality and reducing time-to-market. The operational impact has been a significant reduction in design errors and improved efficiency.
Meanwhile, General Electric (GE) leveraged Asset Twins to monitor and maintain their wind turbines. By integrating real-time sensor data and historical performance data, GE could predict maintenance needs and prevent downtime. This real-world application resulted in a 20% increase in turbine uptime, showcasing clear industry success.
In another example, Unilever applied Process Twins to optimize their production lines. Using advanced simulations, they identified bottlenecks and optimized workflows, leading to a 15% increase in productivity. Their performance results highlight the operational impact of implementing digital twins in process management.
Let’s break down some key examples in a table for clarity:
Company | Type of Digital Twin | Implementation Strategies | Operational Impact | Performance Results |
---|---|---|---|---|
Siemens | Product Twins | Simulate and optimize design | Reduced design errors | Improved efficiency |
General Electric | Asset Twins | Real-time monitoring and maintenance | Increased turbine uptime | 20% uptime increase |
Unilever | Process Twins | Workflow optimization | Reduced bottlenecks | 15% productivity increase |
BMW | Factory/Plant Twins | 360-degree facility view | Enhanced operational oversight | Streamlined operations |
Procter & Gamble | Supply Chain Twins | Real-time supply chain monitoring | Improved decision-making | Reduced supply chain risks |
These examples showcase the clear benefits and measurable performance results of digital twins in various real-world applications, demonstrating industry success and robust implementation strategies.
Challenges and Solutions for Digital Twin
Implementing digital twins in manufacturing presents several challenges, but targeted solutions can effectively address these hurdles. One of the primary implementation hurdles is data integration. You’ll need to consolidate data from disparate sources such as IoT sensors, ERP systems, and legacy databases. Employing robust holistic middleware solutions can streamline this process, ensuring seamless data flow and integrity.
Scalability concerns often arise when attempting to deploy digital twins across large-scale operations. To tackle this, utilize cloud-based platforms that offer elastic scalability. These platforms can dynamically allocate resources, thereby accommodating the increasing volume and complexity of data without compromising performance.
Organizational resistance is another significant barrier. Integrating digital twins requires a cultural shift and buy-in from all stakeholders. You can mitigate resistance through thorough training programs and clear communication about the benefits and long-term ROI of digital twin technology. Highlighting success stories and pilot project outcomes can also foster acceptance.
Cost considerations aren’t to be overlooked. Initial investments in hardware, software, and training can be substantial. However, performing a detailed cost-benefit analysis can help justify these expenditures. Focus on the potential for reduced downtime, optimized maintenance schedules, and improved product quality, which can offset the upfront costs over time.
Future Trends
As we look ahead, the integration of advanced technologies like AI and blockchain will redefine the capabilities and applications of digital twins in manufacturing. AI integration will enhance predictive analytics, enabling more precise forecasting and proactive maintenance. You’ll see real time collaboration become the norm, with stakeholders across the supply chain accessing and interacting with digital twins simultaneously, driving faster and more informed decision-making.
The shift to a circular economy will be facilitated by digital twins, which will optimize resource usage and waste management. By simulating product lifecycles, manufacturers can design for durability and recyclability, guaranteeing minimal environmental impact. Personalized supply chains will also emerge, with digital twins enabling highly customized production processes tailored to individual customer needs. This transformation will enhance responsiveness and flexibility, allowing you to deliver bespoke products with unprecedented efficiency.
On demand logistics will transform, driven by digital twins that provide real-time visibility and control over logistics networks. By simulating various scenarios and optimizing routes, digital twins will reduce lead times and improve delivery accuracy. The seamless integration of AI and blockchain in these systems will safeguard data integrity and transparency, fostering trust and collaboration among partners.
Moreover, end-to-end digital twins will provide a holistic view of the entire supply chain, from raw materials to finished products. This all-encompassing oversight will enable you to anticipate disruptions, optimize inventory levels, and enhance overall operational efficiency. As these technologies evolve, the manufacturing landscape will become more agile, sustainable, and customer-centric, paving the way for a future where digital twins are indispensable tools for innovation and competitiveness.
Frequently Asked Questions
How Do Digital Twins Integrate With Existing Manufacturing Systems?
You integrate digital twins with existing systems by ensuring system interoperability, enabling real-time updates, and facilitating predictive maintenance. Optimize workflows and seamlessly integrate legacy systems to enhance overall efficiency and performance in your operations.
What Data Sources Are Essential for Creating an Accurate Digital Twin?
To create an accurate digital twin, you’ll need sensor data, machine logs, CAD models, IoT devices, and operational metrics. Integrating these data sources guarantees your digital model reflects real-time operations and optimizes performance effectively.
How Long Does It Take to Implement a Digital Twin in Manufacturing?
To determine the implementation timeline, you’ll need to take into account pilot projects, resource allocation, change management, and software selection. Typically, it takes several months to a year, depending on complexity and readiness of your organization.
What Are the Cybersecurity Risks Associated With Digital Twins?
You face cybersecurity risks like data breaches, insider threats, phishing attacks, ransomware incidents, and network vulnerabilities. These issues compromise your digital twin’s integrity, disrupt operations, and can lead to significant financial and reputational damage.
How Can Small Manufacturers Afford Digital Twin Technology?
You can afford digital twin technology by leveraging cloud solutions, forming vendor partnerships, exploring financing options, and seeking government grants. Scalable software guarantees you only pay for what you use, maximizing cost efficiency.
Start today, pivot tomorrow
By embracing digital twins, you’ll revolutionize your manufacturing processes with real-time monitoring, predictive maintenance, and optimization. These virtual replicas drive efficiency, reduce downtime, and enable data-driven decision-making.
With AI and blockchain integration on the horizon, digital twins promise even more precise forecasting and collaborative decision-making. Stay ahead of the curve by leveraging these advanced technologies to achieve significant cost savings and sustainability initiatives.
The future of manufacturing is digital—don’t get left behind.