Digital Transformation (DT) is the integration of digital technologies into all facets of production, fundamentally changing how manufacturers operate and deliver value to customers. It’s not just about adopting new tech but reshaping entire business models to leverage the full potential of the digital age.
Now, why is reskilling the workforce crucial for a successful DT? As cutting-edge technologies like AI, IoT, and advanced robotics become commonplace, the skillsets required to utilize these tools effectively are changing. Workers equipped with traditional manufacturing skills must adapt to the new digital landscape to stay relevant and propel their organizations forward.
In this article, we’ll dive into essential topics for reskilling in manufacturing: data skills, digital literacy, efficiency, sustainability, human-machine collaboration, effective training, and change management. Buckle up—it’s time to prepare your people for the digital revolution.
Understanding Digital Transformation in Manufacturing
Digital transformation in manufacturing isn’t just about adopting new technology; it’s about fundamentally changing how a factory operates. Think of it as giving the entire production process a technological makeover. From using advanced robotics and artificial intelligence to implementing Internet of Things (IoT) devices, digital transformation aims to make manufacturing more efficient, agile, and data-driven.
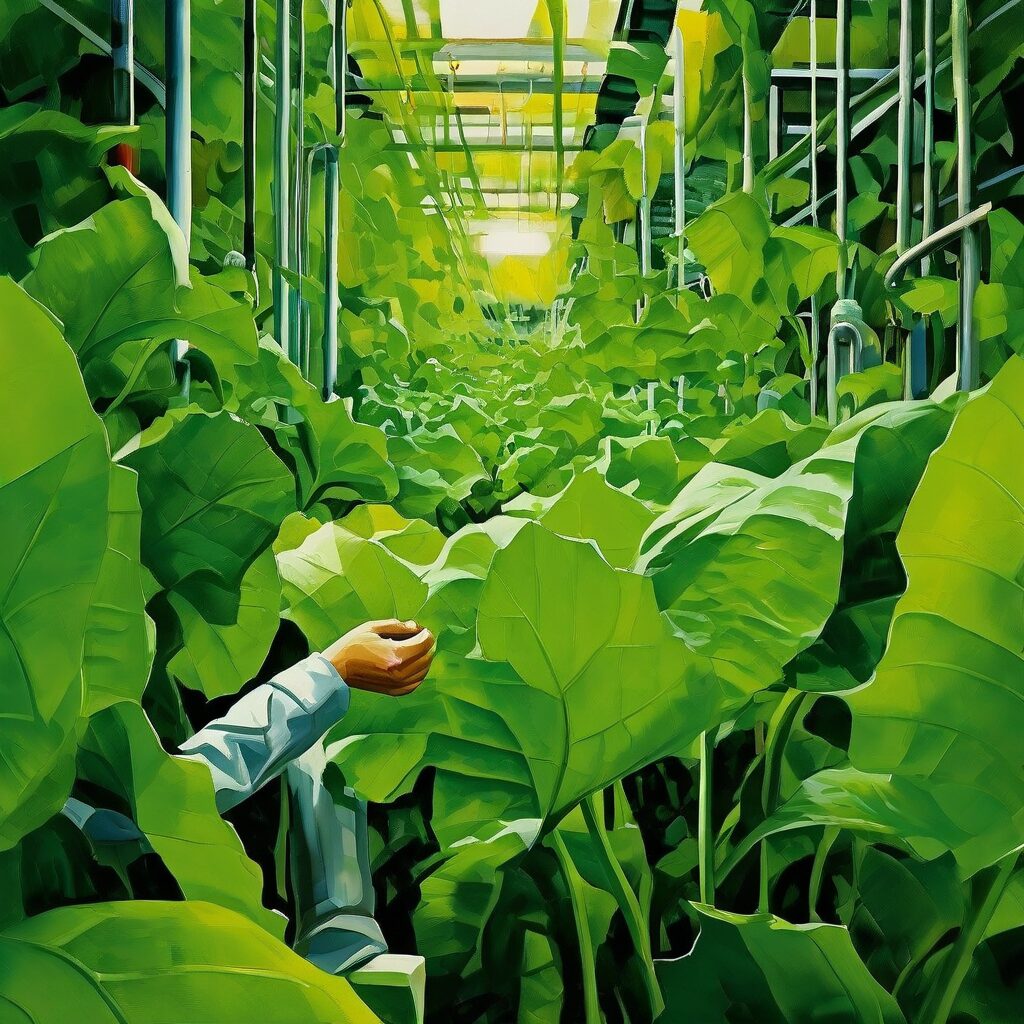
Key Components
- Knowledge Platforms
- Advanced Robotics
- Artificial Intelligence (AI)
- Internet of Things (IoT) Devices
Key Drivers of Digital Transformation
These factors together are pushing manufacturing into a new digital era, and companies that don’t adapt may struggle to survive.
Technological Advancements
Technological advancements are snowballing—AI and machine learning are not just buzzwords but actual game-changers.
Competitive Pressure
Competitive pressure plays a significant role; manufacturers need to stay ahead or risk becoming obsolete. Consider calculated risks
Efficiency Gains
Efficiency is the golden egg. Automation can trim down production times and reduce human errors, giving the company a significant edge.
Why Reskilling is Essential for Digital Transformation
Manufacturing is facing a shift as digital transformation becomes more deeply embedded within industry operations. With technology advancing at a breakneck pace, the need to equip the workforce with new skills is more critical than ever. Here’s why reskilling needs to be a priority:
Data Skills and Digital Literacy
As manufacturers integrate more digital tools, the ability to interpret and analyze data becomes essential. Workers need to migrate from traditional methods to data-driven decision making. Understanding metrics, predictive maintenance, and real-time monitoring are no longer optional; they are required competencies. As noted by McKinsey, companies that invest in digital skills training are better positioned to compete and thrive.
Efficiency Gains
Reskilling can lead directly to enhanced efficiency. Digital tools allow for streamlined operations, minimizing downtime, and optimizing workflows. Employees who are adept with these technologies can identify bottlenecks and implement fixes in real time, significantly improving overall productivity.
Sustainability Goals
With sustainability becoming a cornerstone of modern manufacturing, digital skills are crucial for implementing energy-saving practices and reducing waste. Knowledge of IoT and smart manufacturing systems enables workers to fine-tune production lines for minimal environmental impact, aligning with broader corporate sustainability goals.
Reskilling the workforce is not simply an added bonus but a necessity for any manufacturing company aiming to remain relevant and competitive during this digital era. The investment pays off in spades—through efficiency, sustainability, and a future-ready workforce.
Key Areas for Workforce Reskilling
Data Skills
In today’s manufacturing landscape, the ability to analyze and interpret data is central. Companies are awash with data, but without the skills to harness and interpret this information, it remains untapped potential. Workers need to be adept at basic data analysis, understanding metrics, and utilizing tools like Excel or specialized manufacturing software. On the advanced end, proficiencies in big data analysis, machine learning algorithms, and predictive maintenance will set employees apart, enabling them to drive innovation and efficiency within the manufacturing process.
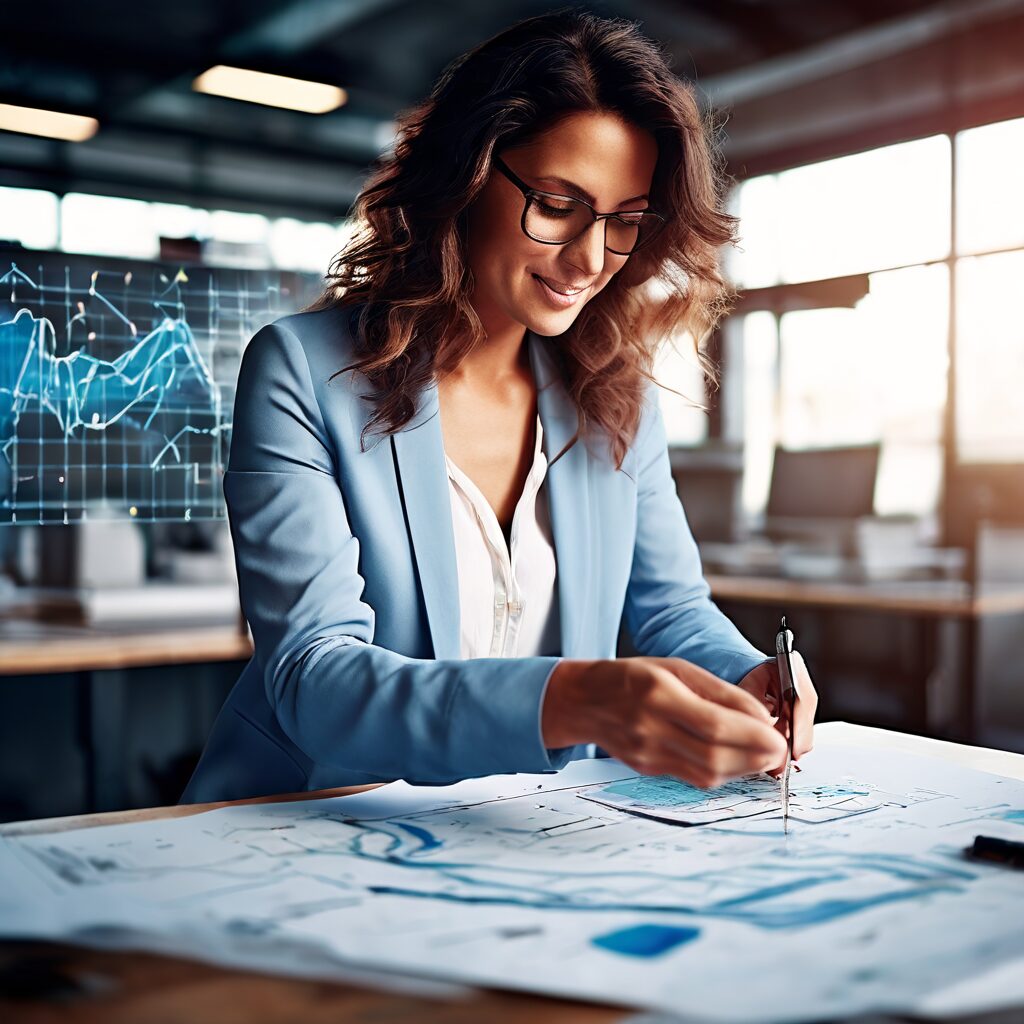
Digital Literacy
Digital literacy extends beyond knowing how to use a computer. It encompasses understanding how to navigate digital tools and platforms specific to the manufacturing sector effectively. Workers must get comfortable with Manufacturing Execution Systems (MES), Enterprise Resource Planning (ERP) software, and Internet of Things (IoT) devices. This digital fluency ensures that employees can optimize production lines, manage supply chains in real-time, and integrate new technologies seamlessly into existing workflows.
Efficiency
Digital tools have the power to drastically streamline manufacturing processes. For instance, employing predictive maintenance algorithms can foresee equipment failures before they happen, reducing downtime. Automated quality control systems ensure consistent product standards with less manual inspection. By reskilling workers to handle these tools, manufacturers can realize significant efficiency gains. These improvements translate to faster production times, reduced waste, and overall cost savings.
Sustainability
Digital transformation can also play a crucial role in enhancing sustainability in manufacturing. Workers skilled in using data-driven insights can fine-tune production processes to minimize waste and maximize resource efficiency. For example, IoT sensors can monitor energy consumption in real-time, allowing for immediate adjustments to reduce the carbon footprint. By marrying digital skills with a commitment to environmental responsibility, manufacturers can achieve sustainability goals without compromising productivity.
Human-Machine Collaboration
The integration of AI and robotics in manufacturing necessitates a shift in how employees view their roles alongside machines. Rather than replacing human labor, these technologies are designed to augment it. Workers should be trained to understand and manage collaborative robots (cobots) and AI-driven systems. This involves not only technical know-how but also fostering a mindset that sees these machines as partners in the production process. By preparing workers for this symbiotic relationship, manufacturers can harness the full potential of human-machine collaboration, leading to safer, more efficient, and innovative manufacturing environments.
Strategies for Effective Training
So you’ve decided it’s time to reskill your workforce to conquer the digital age in manufacturing. Great. But what’s the best approach to training that doesn’t just tick the boxes but truly transforms? Here’s a playbook that sidesteps the fluff and gets down to business.
Practical Steps for Implementing Effective Training Programs
First thing’s first: assess your needs and workforce capabilities. It sounds basic, but you need a clear understanding of the skills gap before you can fill it. Use skills assessments, feedback surveys, and performance reviews to get a concrete picture.
With gaps pinpointed, tailor your training programs—one-size-fits-all won’t cut it. Use a mix of online courses, hands-on workshops, and peer-to-peer learning. For tech-driven skills, focus on real-world applications. Think simulations for machine operations, or data analysis exercises with actual manufacturing data.
Leverage internal talent. Your existing experts can mentor or lead workshops, making the training relatable and practical. Plus, this boosts morale and reinforces the learning culture.
Continuous Learning and Development
Training isn’t a one-and-done deal. The digital landscape shifts quickly. Establish a culture of continuous learning. Encourage regular updates to skills through workshops, webinars, and certification courses. Make sure these opportunities are accessible – online platforms offer flexibility and broad reach.
Create a feedback loop. Regularly check in on the efficacy of training programs. Are employees implementing what they’ve learned? Use these insights to refine and improve ongoing training efforts.
Expert Insight
It’s useful to turn to proven strategies. According to insights from Pivot Digital Transformation, effective training requires a balance of technical skills development and soft skills enhancement like problem-solving and adaptability.
Engaging Training Content
Effective training also hinges on engaging content. Dull PowerPoint slides won’t cut it. Integrate interactive elements like AR/VR for virtual plant tours or 3D modeling. Gamify learning modules to inject competition and motivate employees.
Monitor Progress and Adapt
Finally, keep tabs on progress. Use analytics to measure training outcomes and ROI. Are efficiency and productivity improving? Are employees more comfortable with digital tools? Use this data to fine-tune future training programs.
By implementing these strategies, you ensure your workforce isn’t just hanging on through the digital transformation—they’re driving it. Train smart, stay adaptable, and keep learning.
Change Management in Digital Transformation
Change management is the backbone that keeps digital transformation efforts from unraveling. It essentially involves preparing, equipping, and supporting individuals to successfully adopt change to drive organizational success. Within the manufacturing sector, where traditional processes often run deep, managing this shift is crucial for any reskilling initiative to work.
So why is change management so vital? Simple. People naturally resist change, especially when it threatens their routine or job security. Here’s the kicker: A structured approach to change management can mitigate resistance and promote a culture amenable to digital advancements.
First off, leadership alignment is key. Leaders must be on the same page, expressing a unified vision of the digital future they see for the organization. This paves the way for clear and consistent communication across all levels of the company. Employees need to understand not just the ‘what’ and ‘how’ of the changes, but also the ‘why’. Break it down: show them how new skills and digital tools will enhance their roles and make their jobs easier, not redundant.
Now, let’s address resistance head-on. Resistance can come in many forms—fear, skepticism, or plain inertia. Identifying these early allows for targeted interventions. One effective strategy is involving employees in the change process. Make them stakeholders rather than mere recipients of change. Soft skills like empathy and active listening can go a long way here. Also, recognize and celebrate quick wins to build momentum and morale.
Cultivating a culture of continuous learning is another critical factor. Digital transformation isn’t a one-and-done project; it’s an ongoing journey. Promoting a mindset of agility and adaptability ensures that the workforce remains dynamic and responsive to future technological shifts. Promote internal forums, workshops, and knowledge-sharing sessions that keep the learning engine running.
Lastly, don’t underestimate the power of training programs tailored for change management. Equip your team leaders with the tools to manage their squads through transitions effectively. A well-supported leader can inspire their team to embrace new challenges enthusiastically.
In summary, change management could very well be the linchpin of your digital transformation journey. By tackling resistance, fostering a learning culture, and ensuring clear communication, you position your workforce to adapt and thrive in an evolving digital landscape. For more on realizing true ROI in digital transformation, check out these insights from Pivot Digital Transformation.
Start today, pivot tomorrow
Reskilling the workforce is not just a necessity, but a strategic imperative for the successful execution of digital transformation in the manufacturing sector. In an industry rapidly evolving through technological advancements, competitive pressures, and the drive for greater efficiency, equipping your people with new data skills and digital literacy is crucial.
The journey towards digital transformation should be a shared effort, integrating advanced data skills, digital literacy, efficiency, sustainability, and human-machine collaboration into the fabric of everyday work. As employees become proficient across these areas, manufacturing operations will not only become more efficient but also more sustainable and innovative.
Effective training programs tailored to continuous learning and embracing change are key. Organizations must commit to fostering an adaptable and future-ready workforce. By doing so, they not only pave the way for successful digital transformation but also secure a competitive edge in an increasingly digital world.
Encourage your team to embrace the new digital tools and methodologies. Support their efforts with comprehensive training and change management strategies. In this way, you are not just preparing your workforce for the future of manufacturing—you are building a resilient, progressive, and forward-thinking organization.
[…] develop talent and skills effectively, start by identifying the specific competencies required for your digital transformation goals. Use […]